Drive Efficiency And Innovation In Automotive Industry
The automotive industry is highly competitive, with a constant need for increased production efficiency, optimized supply chains, and stringent compliance with quality standards. Manual processes such as inventory management, supplier coordination, production tracking, and regulatory reporting can slow down operations and lead to errors.
gNxt Systems, we provide industry-specific Robotic Process Automation (RPA) solutions that help automotive companies streamline operations, reduce costs, and improve accuracy. By automating repetitive and labor-intensive tasks, automotive companies can focus on innovation, reduce downtime, and enhance overall production efficiency.
Key Benefits of RPA in the Automotive Industry
Key Benefits of RPA in the Automotive Industry

Enhanced Production Efficiency
RPA automates routine manufacturing tasks, improving production line speed, reducing delays, and minimizing downtime.

Cost Savings
Automating high-volume, repetitive tasks helps reduce operational costs, allowing manufacturers to optimize resources and improve margins.

Improved Accuracy
RPA ensures accuracy in inventory management, production tracking, and quality control by eliminating manual errors.

Supply Chain Optimization
Automating supplier coordination and logistics ensures a smooth, efficient, and reliable supply chain.

Scalable Operations
RPA solutions scale easily to accommodate increasing production volumes and new automotive models.
Estimate RPA's financial impact easily with our ROI calculator
Enhancing Automotive with RPA
Enhancing Automotive with RPA
1. Inventory Management & Tracking
Managing parts and materials in automotive manufacturing requires real-time visibility and accuracy. RPA automates inventory tracking, stock level updates, and reordering, ensuring that you always have the right materials on hand.
- Automate inventory tracking to keep stock levels updated in real time.
- Trigger automated reorders when stock falls below a set threshold.
- Generate inventory reports for better resource planning and decision-making.
2. Supplier Coordination & Procurement
Coordinating with suppliers and managing procurement processes can be time-consuming. RPA can automate supplier communications, purchase order creation, and invoicing to streamline procurement and improve relationships with suppliers.
- Automate purchase order creation and approval processes.
- Facilitate seamless supplier communication for order updates and confirmations.
- Generate automated reports on supplier performance and procurement metrics.
3. Production Line Monitoring & Quality Control
RPA can monitor production lines in real-time, detect potential bottlenecks, and automate quality control processes to ensure that production standards are consistently met. This reduces defects and downtime while improving product quality.
- Monitor production lines to identify inefficiencies or delays.
- Automate quality control checks to ensure product compliance with standards.
- Generate production and quality reports for real-time insights.
4. Logistics & Supply Chain Automation
Managing the supply chain and logistics in the automotive industry requires precision and coordination across multiple stakeholders. RPA automates shipment tracking, supplier coordination, and real-time updates to ensure that materials and parts flow smoothly through the supply chain.
- Automate logistics tracking for real-time visibility into shipments.
- Coordinate with suppliers for timely deliveries and reduce lead times.
- Streamline supply chain reporting for better forecasting and planning.
5. Regulatory Compliance & Reporting
Automotive manufacturers must adhere to strict regulatory requirements regarding safety, environmental standards, and production processes. RPA automates the generation of compliance reports and ensures audit trails are maintained for transparency.
- Generate compliance reports automatically for regulatory bodies.
- Maintain detailed audit trails for all production and supplier activities.
- Ensure compliance with environmental and safety regulations through automated monitoring.
gNxt Systems Optimizes Automotive
gNxt Systems Optimizes Automotive
At gNxt Systems, we understand the complexities of the automotive manufacturing process and the need for accuracy, speed, and cost efficiency. Our RPA solutions are designed to address the specific challenges faced by automotive manufacturers and ensure a streamlined, efficient, and compliant operation.

Custom Automation Strategy for Automotive Companies
We start by analyzing your current manufacturing processes to identify automation opportunities that will deliver the greatest impact. Whether it’s optimizing your supply chain or automating quality control, we create a custom RPA strategy to fit your needs.
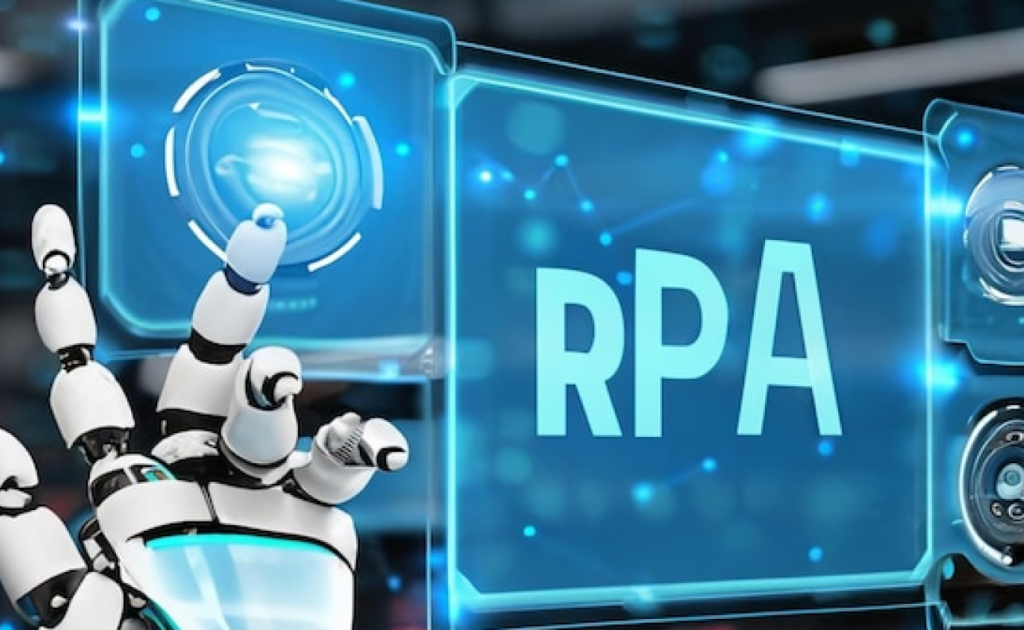
Seamless Integration
Our RPA solutions integrate seamlessly with your existing Manufacturing Execution Systems (MES), Enterprise Resource Planning (ERP) platforms, and other automotive software. This ensures that automation enhances your workflows without disrupting production.

Expert Implementation & Continuous Support
From initial bot development to deployment and ongoing optimization, our RPA experts manage the entire implementation process. We continuously monitor and refine the bots to ensure your automotive operations remain efficient, accurate, and scalable.
Start Your RPA Journey: Schedule No-Cost Guidance Session​
Case Studies
Case Studies
Streamlining Supply Chain Management
Challenge:
A regional supplier of automotive parts to local manufacturers and repair shops faced inefficiencies in their supply chain management process. Their team manually updated inventory levels, processed orders, and coordinated with suppliers, leading to frequent stock discrepancies, delays in order fulfillment, and increased operational costs.
Solution:
The company deployed RPA to automate key supply chain functions. RPA bots monitored inventory
levels in real-time, automatically reordering stock when thresholds were met and generating
purchase orders for suppliers. The bots also handled invoicing and order processing, cross-
referencing incoming orders with inventory availability.
Outcome:
- 90% Improvement in Stock Accuracy due to the elimination of manual errors in inventory management.
- 60% Faster Order Processing, enabling the company to fulfill customer requests more efficiently.
- 20% Reduction in Operational Costs through the automation of order management processes, minimizing manual intervention.
Enhancing Customer Service Through RPA
Challenge:
A small automotive electronics manufacturer struggled to manage customer inquiries and warranty claims efficiently. The customer service team was overwhelmed with repetitive tasks such as answering product inquiries, processing warranty claims, and tracking orders, which slowed response times and reduced customer satisfaction.
Solution:
The company implemented RPA to automate customer service workflows. RPA bots were integrated into the customer service platform to handle routine inquiries, process warranty claims, and send order updates to customers. The bots interacted with customers via chat and email, allowing human agents to focus on more complex and high-priority tasks.
Outcome:
- 50% Improvement in Response Times, leading to higher customer satisfaction rates.
- Increased Efficiency, as RPA reduced the workload on customer service agents, allowing them to manage more inquiries without additional staffing.
- 40% Faster Claims Processing, resulting in quicker resolutions and improved customer trust.
Schedule No-Cost Guidance Session
Schedule No-Cost Guidance Session
Contact us today for No-cost personalized guidance session or more information.